Semi-Automated Pallet Shuttles Support Denser DC’s, Enhance Productivity
Using automation to create a denser use of distribution center cubic space and reduce labor needs is not a new concept. Neither is the thought that the only way to realize significant benefits is with full-on automation. Luckily that’s not the case. You can realize the benefits of automation by using automated carts or pallet shuttles that position pallet loads at the pick faces, reducing the need for aisles and lessening the time needed to place and remove products.
These semi-automated solutions have been around for years and are now becoming cost effective for a wider segment of distribution centers – those with around 1,000 pallet positions or more, notes Ryan Wachsmuth, Southeast Regional Sales Manager for Steel King Industries. So, for every thousand pallet positions, you’d engage an automatic shuttle and realize a very high rate of productivity.
As distribution centers get larger and as demand to optimize use of a facility’s cubic space gets greater, pallet shuttles are a smart way to help achieve optimal productivity. Lanes can be very deep – only constrained by the square footage of the facility and the logistics of moving the pallet loads. If, for example, you can load a truck with product in a lane 30 positions deep, you can design the shuttle lane to be 30 pallets deep.
Pallet Carts Boost Productivity
Automated pallet carts perform the deep lane transport, freeing the lift truck operator to travel only between load source and lane entry. That maximizes productivity and minimizes operator travel distance. With every slot in the racking programmed, the cart knows how to position each load to provide the required load separation.
“Users really like the benefit of the automated pallet positioning,” Wachsmuth said. “They don’t have to retrieve the load from within the system; the pallet cart is doing that for them.” For systems where loads are added on one side and removed on the other, there’s always a load at the face of the discharge side, optimizing handling efficiency. It also reduces the risk of impact damage to the rack structure and to the stored product.
The reduced amount of labor required for load handling gives pallet shuttles it advantages over drive-in, push-back and pallet flow systems, notes Bill Edgy, Director of National Accounts for Automha Americas, an international pallet shuttle cart manufacturer that is now collaborating with Steel King to incorporate its Pallet RunnerTM deep lane storage system to Steel King’s client and distributor base. Pallet Runner can be added to any type of Steel King pallet racking.
Advantages Over Non-Automated Systems
Impact damage is inherent with drive-in systems and they can require a lot of repositioning to get to the desired pallet loads. Push-back systems can lead to product damage. And pallet flow systems reduce usable vertical space because of the slope they require. In cold storage facilities, impact damage is more likely due to density and the effects of cold temperatures on lift operators. Edgy notes that is one reason that about a third of Automha Pallet Runner installations are in the cold storage sector. The units operate amid temperatures down to -22 degrees. (Units can be built with stainless steel components and a sealed battery housing to allow for use in wet environments.)
The Pallet Runner also can help a facility comply with fire safety standards, according to Edgy. “Insurers such as FM Global are strictly following an NFPA recommendation calling for a six-inch separation of loads where in-rack fire suppression systems don’t exist,” he says. With non-automated storage systems, an operator could use pallet separators, to create the needed separation, but Edgy notes that those tools often don’t work or are overly cumbersome to put in place. In contrast, the Pallet Runner can be programmed to automatically position pallets with the fire-safety-required separation. Separation space can be set from 25 mm to 250 mm (about 1 to 10 inches.)
Experience-Based Reliability
While there are other pallet shuttle manufacturers, Wachsmuth noted Automha America’s extensive experience as a factor in positioning it as a shuttle of choice. “Potential users should not only look at what features are available, but also the generation of the cart,” he says. “Automha Americas is on its 10th generation, meaning there have been a lot of advancements since it was originally released, and meaning that it excels in reliability. Other manufacturers are only third generation or younger in their versions.”
Users have high praise for the system, notes Edgy, adding that he’s never had a Pallet Runner system removed. “It’s a significantly different way to handle pallet loads, but once our system is up and running, users find themselves asking: ‘How did we get by without this all these years?’,” Edgy said.
Each Pallet Runner system is designed for the specific dimensions of the pallet racking structure and the dimensions of the pallets used in that operation, whether than be 40×40, 40×48 or other. The carts can handle pallet loads weighing up to 4,400 pounds (2,000 kilograms) and have safety features to protect personnel and product. They are compatible with all common North American lift trucks.
Pallet Runners add value to a wide variety of material handling applications, including cold storage and freezer warehouses mentioned above. Other sectors include food and beverage, pharmaceutical, retail and e-commerce, and manufacturing.
If you’re operating a distribution center with a high volume of SKUs, a Pallet Runner system can take your operating efficiency to the next level. You’ll make better use of your cubic space and more efficiently handle pallet loads.
SOLUTIONS FOR EVERY INDUSTRY.
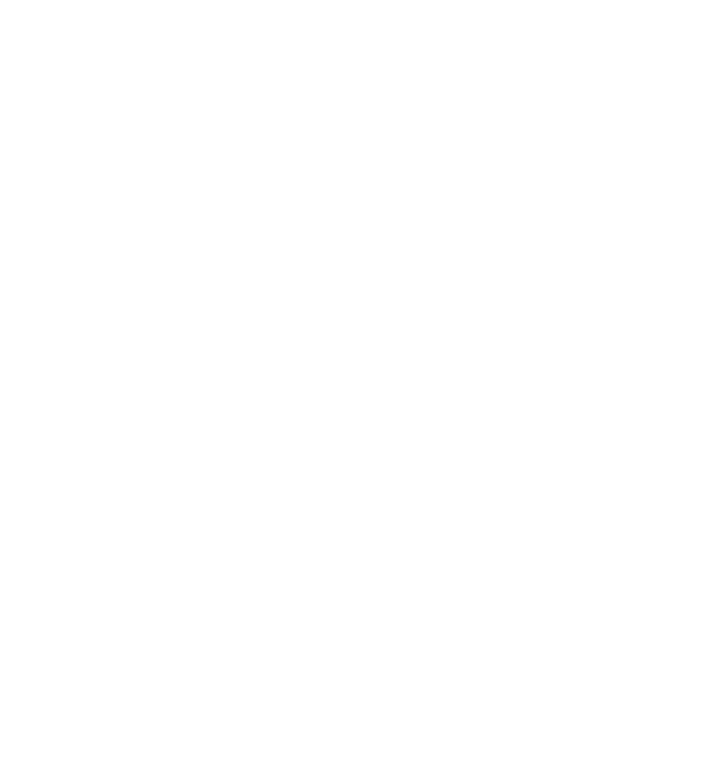
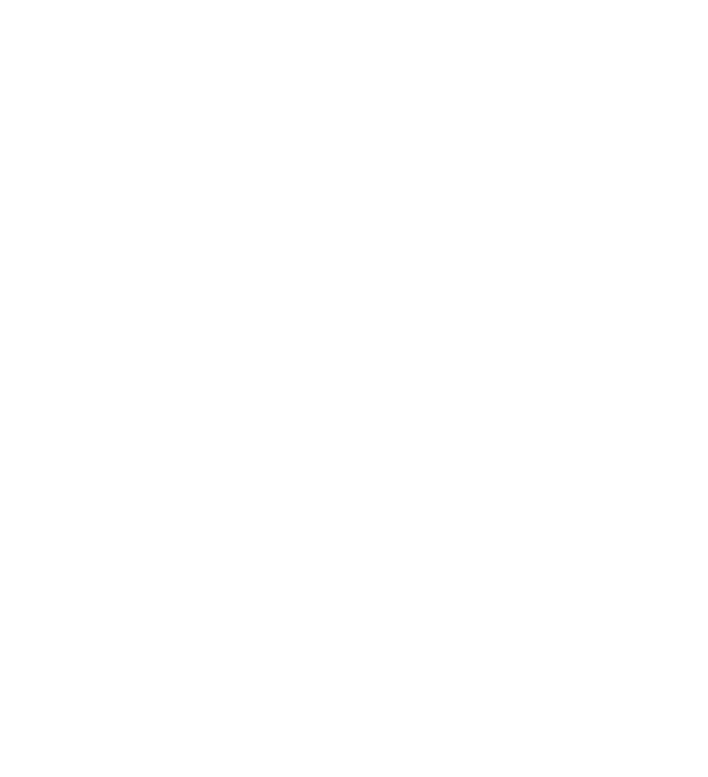
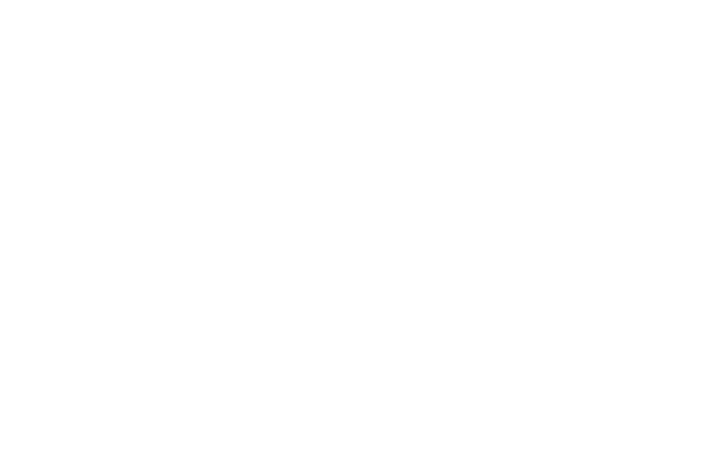