Keep Your DC Running Safely and Smoothly with Safety Gates
Easy and safe access to product and equipment is a fundamental need of distribution centers and other material handling facilities. Safety gates – designed and manufactured in a variety of configurations, provide that access.
“With the constant movement of product in a distribution center, and the need to reach equipment, ease of access is essential for top productivity, but that access needs to be controlled to protect personnel and, in some cases, to make sure access to equipment is limited,” according to James Augustyniak, Midwest Regional Sales Manager for Steel King Industries.
Safety gates are especially important on mezzanines and platforms for fall protection, but they also play a role in safety at the ground level, Augustyniak noted.
Swing gates allow for controlled and access at floor and upper levels. Pivot gates are widely used on distribution center work platforms where forklifts are placing pallet loads. Both types are usually manually controlled, but automated gates are an option in some instances.
Swing gates are used at any level for safety and access control. As the name implies, these gates swing open. Manual gates are self-closing via springs which can be adjusted for tension control. These gates are sometimes called pedestrian or forklift crossing gates. Slide gates are similar in function to swing gates but slide horizontally in line with guard railing rather than swinging open.
Swing and slide gates – some lockable, also are used to limit access to equipment. Automated versions are available, some with motion sensors. Swing gates are generally part of a guard rail system, but they can be installed independent of the railing.
Steel King manufactures swing gates to the same level of durability as our Steel Guard heavy duty railing and Armor Guard medium duty protective railing. The heavy-duty version is the most common, while the medium duty version is typically used where medium-duty railing delineates work cells or other such areas.
Steel Guard and Armor Guard gates are designed to fit a 48” post-to-post center line within a protective railing system, with the standard size (38-1/2” tall and 43-3/4” wide) being available through Steel King’s Quick Ship program.
Compared to other gates on the market, Steel King’s heavy-duty version has a more solid construction, with more steel and a design that withstands forklift impacts. They are made with American steel.
A sufficient number of swing or slide gates should be installed so personnel are not tempted to climb over guard railings, Augustyniak advises.
Steel King’s swing gate can easily be reversed by unbolting the gate and switching it from the left to the right post, or vice versa.
Pivot gates, sometimes called pallet gates, pallet access gates or mezzanine gates, maintain a barrier on mezzanines when pallet loads are being placed or pallets are being retrieved. These usually have a simple design, allowing the user to easily create an area for a pallet load to be placed while maintaining fall protection for personnel.
“When the front gate is opened, the back gate pivots down, creating a quarantined area where the load can be placed or retrieved,” said Chris Pahls, Product Manager at Steel King’’s NexCaliber Structures platform division.
Pivot gates manufactured by Steel King include a bearing at the pivot point which supports a smooth open-and-close process, Pahls says. Further, he notes, the simplicity of the Steel King pivot gate requires less maintenance than other manual or automatically activated pivot gates available.
“Pivot gates are used constantly in use in distribution centers, so you want them to be in working shape all the time,” says Pahls. “Some pivot gates have a lot of parts and aren’t as durable, which leads to productivity disruptions when there is a problem.”
An option offered by some manufacturers allows a forklift driver to automatically pivot the gate.
Ladder gates, which OSHA requires to be placed at the top of a ladder, are designed to prevent falls down the ladder or a staircase.
Loading dock gates are used to create a safe environment where product is being brought into or shipped out of the facility. A variety of styles are available, including swing, swivel, sliding, vertical lift, and folding – in manual or automated versions.
Gate Selection Criteria
When working with a gate provider, there are several factors to discuss to ensure you get the right safety gates for your facility and its material handling needs. Gates are commonly part of a guard rail design when a distribution center is being outfitted with racking, but gates can be retrofitted into existing guard rail.
Design and style of pivot gates is driven by the type of materials being handled. Pahls notes that not all product is on standard 40×48-inch pallets, so a buyer needs to work with a provider that can design a system that will accommodate non-standard loads.
Compliance with OSHA guidelines and IBC codes is essential. While safety gates are not always required at some operating points, Pahls notes that OSHA requires the use of body harness systems with lanyards and connectors, for fall protection if gates are not used.
Ruggedness and durability are important to alleviate maintenance needs and to withstand forklift impacts. Augustyniak notes that Steel King’s swing gates are designed to accept the same level of impact as does its heavy-duty guard rail, using 11-gauge, corrugated steel with three layers of ribbing. Pahls advises use of pivot gates that can be attached to a platform’s deck without support from adjacent guard railing, and which has a steel skid plate to protect the decking material. Gates with powder paint coating will keep their appearance longer.
Gates should be easy to operate and maintain. While automation might make a gate easy to use, those types of gates will have more parts and, thus, will require more maintenance. The ability to easily switch the hinge side of a swing gate is also an ease-of-maintenance issue. “Ease of operation cannot be understated as a factor in choosing safety gates,” according to Pahls.
When planning a material handling facility, make sure safety gates are part of the design process. You can keep your operation running smoothly and safely with the proper selection and use of safety gates, and the proper installation and maintenance of that equipment.
SOLUTIONS FOR EVERY INDUSTRY.
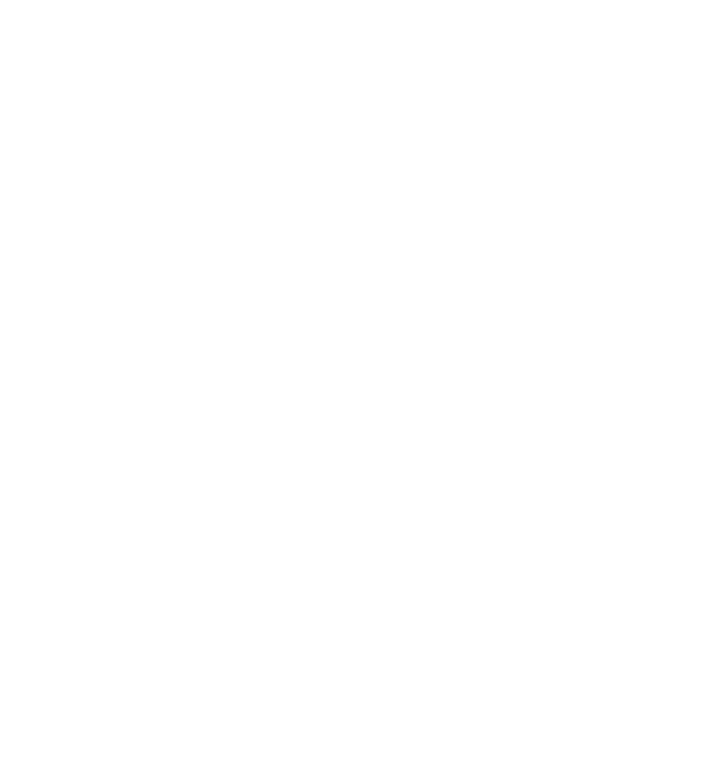
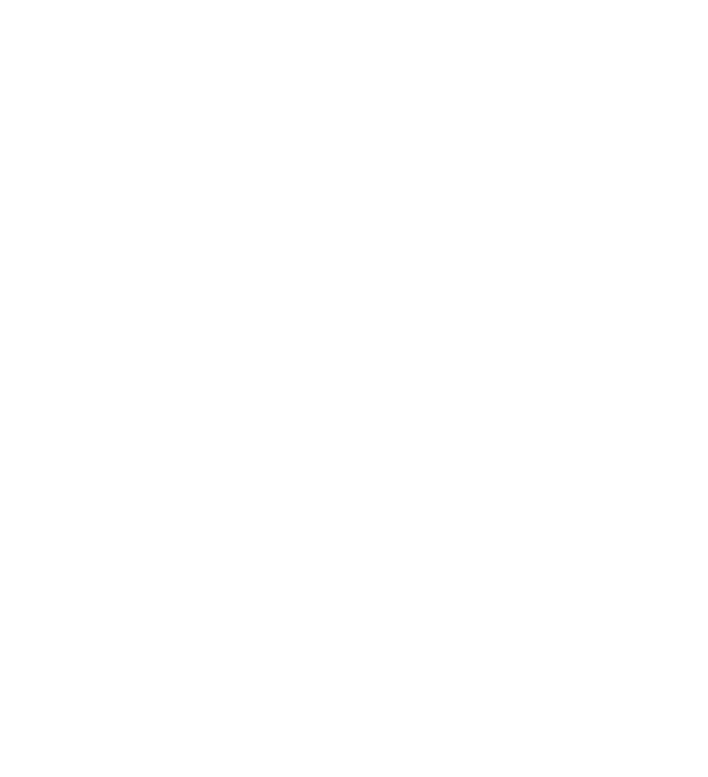
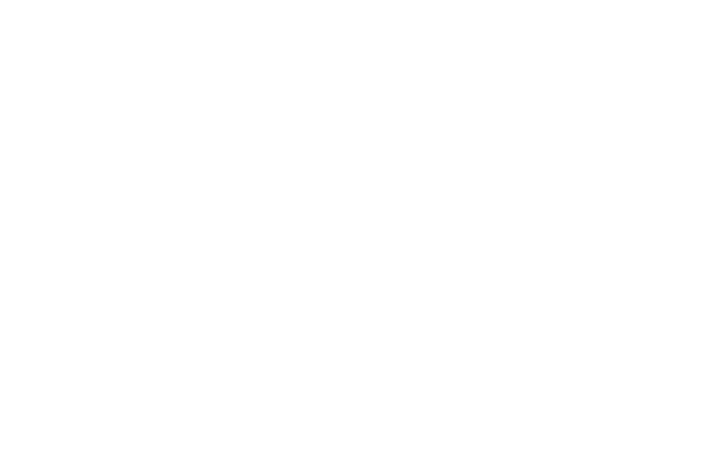
Questions? Contact UsContact Us