Steel King Selective Racking Systems to Bring New Efficiencies to North Pole Warehouse and Fulfillment Centers
A one-of-a-kind fulfillment center – with a unique timeline for picking, packing, and magically delivering orders worldwide within a 12-hour timeframe, has selected Steel King for the new selective pallet racking system for its North Pole warehouse and distribution facilities.
“We needed pallet racking systems that are designed for optimal supply chain efficiency, and that can withstand our annual period of intense and hectic operations,” said the red-clad, white-bearded CEO of the international organization, who asked to remain anonymous. “Our organization has what is probably the most unbreakable delivery schedule of any logistics operation, and we know the racking experts at Steel King could help design a system that will support our on-time delivery requirements and maximize our storage capacity.”
Selective Racking Systems for Thousands of SKUs
The organization was especially interested in Steel King’s selective racking system, because of the thousands and thousands of SKUs that must be readily available for picking by a seemingly tireless, pointy-eared staff. To accommodate the extremely high volume of many items, Steel King’s flow racks and pushback racks are also part of the contract for installation in the coming year, to allow for greater storage capacity in the North Pole’s fulfillment centers.
The organization’s complex of facilities includes manufacturing operations that provide a steady stream of items needing to be stored after manufacturing – in some cases for nearly a year. Most of the orders that need to be fulfilled arrive in the fourth quarter of each year, but because of the tremendous volume of goods that need to be on hand for international delivery on the night of December 24, planners at the North Pole operation must be experts in market analysis and in identifying trends in consumer demand.
“While we can deliver everything in one night, it takes many months to get our warehouses and fulfillment center packed with toys, computers and gaming items, clothing, jewelry, tools, household goods, and a myriad of other items,” the North Pole CEO said. “For some items such as SUVs and pickup trucks, we contract with other manufacturers and logistics operations for manufacturing and delivery, because it’s hard to fit vehicles in my delivery sacks.”
Most Orders Received the Old-Fashioned Way
The North Pole operations combine thousands of years of logistics experience with today’s supply chain automation and technologies to maintain a 100 percent on-time delivery rate that is the envy of the material handling industry.
Most of the orders are received via hand-written letters or mouth-to-mouth when the CEO and his numerous stand-ins travel the world to meet with children. All those orders are digitized and fed into the North Pole’s intricate supply chain management system.
Even though orders generally come in early enough to process, last-minute orders and change orders keep a North Pole department busy to ensure customer satisfaction. The division is also responsible for ensuring that children’s orders are acceptable to parents.
“I remember when one child asked for a Red Ryder carbine action, 200-shot, range model air rifle, with a compass in the stock,” the North Pole CEO recalled. “I told the kid he’d shoot his eye out, so we had a change order on that request. Turns out his dad bought him the BB gun anyway.”
While most orders come in the old-fashioned way, tracking technology has made its way into the North Pole operations, thanks to the help of NORAD – the North American Aerospace Defense system that volunteers to track the delivery vehicle as it makes its deliveries around the world.
“On the night of December 24, we need to be super-focused on meeting our deadline of delivery before the morning of the 25th, so we appreciate that NORAD has taken on the tracking responsibility.”
Boltless, Tubular Racking Selected for Durability, Ease of Installation
Steel King’s contract with the North Pole calls for numerous systems using SK2000 boltless, tubular pallet racks. The CEO requested the racking in Steel King’s Vista Green and Fire Engine Red to match their company colors.
The rack elements are made from roll-formed steel, which is lightweight but very strong due to its continuously welded, tubular design. The boltless design makes it easy to assemble without tools and allows for the North Pole’s staff to assist in erecting the racking. These systems will be set up for selective picking.
For items that will be manufactured well in advance – especially items that will be in high demand, SK3400 pallet flow, and SK3600 push-back systems will be installed. SK3400 is a gravity flow storage selective racking system that is ideal for first in/first out (FIFO) inventory management, while the SK3600 is a high-density storage system that allows pallets to be stored two-deep to five-deep. Both are high-density systems that optimize the use of floor space.
The Steel King employees and subcontractors who will help install the racking systems in the coming year are sworn to secrecy regarding the exact location of the North Pole operations.
“You can imagine the storage capacity we need,” said the North Pole CEO. “We obviously can’t make everything at the last minute, so we need pallet racking that is designed to optimize storage capacity in our various buildings. We also want durability in racking and safety accessories, because as good as our pointy-eared staff is, they occasionally bump into rack components when driving forklifts through one of our fulfillment centers.”
Steel King can help solve the North Pole’s material handling challenges, but it remains a mystery how the millions of packages it processes fit in a sleigh and are all delivered in one day.
Happy holidays, everyone!
SOLUTIONS FOR EVERY INDUSTRY.
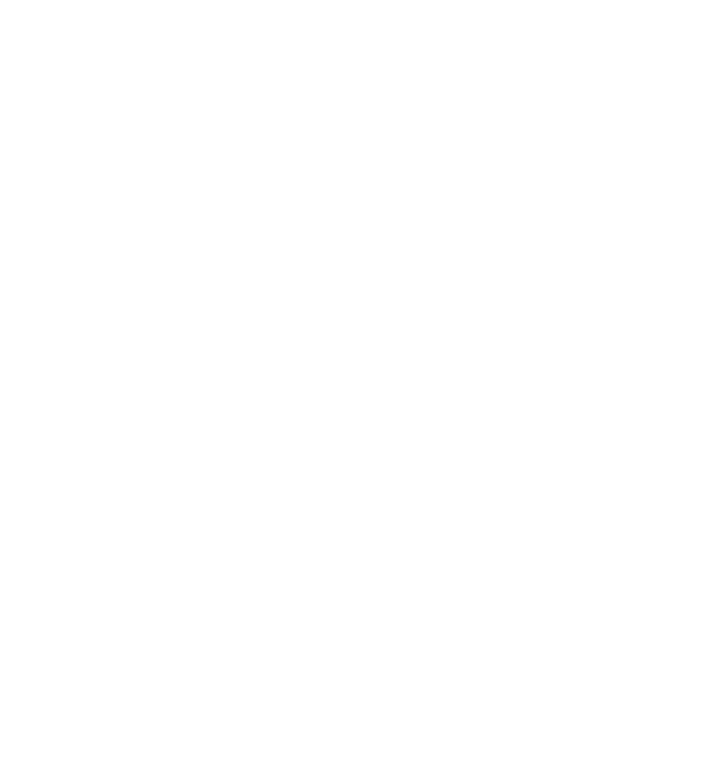
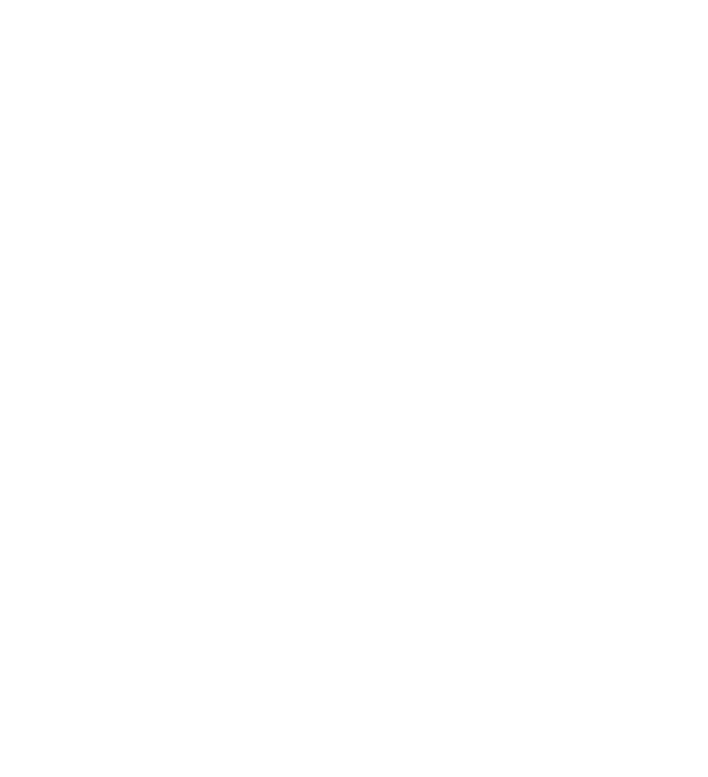
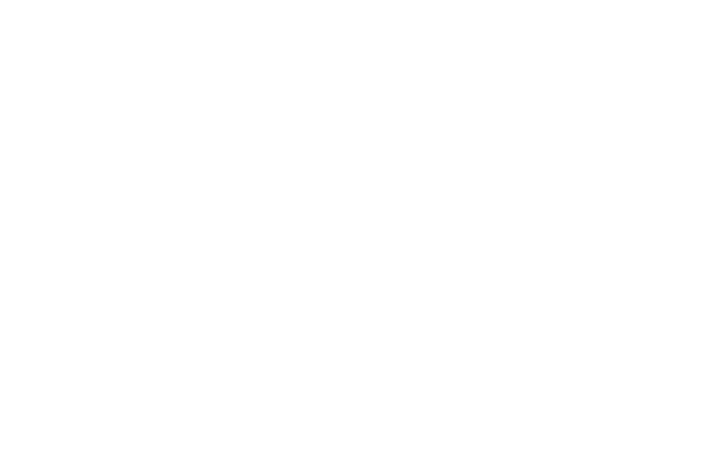